Total.Hydroponic.Control
Active Member
Hello Rollitup, its been a while since I was last here, and consequently, this is a new account. I've been through 5 indoor grows, and 3 outdoor grow seasons. I will start out by saying, that when it comes to growing cannabis I am clearly an amateur. However, I've been working with automation for over 5 years. I am currently employed by a fortune 500 company, and when I wake up everyday I head to work to argue with high speed manufacturing, and process control systems. I'm familiar with Allen Bradley, Automation Direct, Koyo, Omron, Gidding & Lewis, and G.E. PLC's. I eat, breathe, and sleep, automation.
Lately I've been very intrigued with the D.I.Y. automation here on Rollitup. It is clear that RIU is a community of intelligent, driven individuals who are more than willing to share their knowledge and expertise. I applaud all of you who are continually striving to add integrity, knowledge, and ingenuity to the world of marijuana.
This thread is to be my opportunity to share my knowledge on growing, in the manner I am most capable of: Automation.
While many of you have undertaken Arduino projects, with great success, I will be developing a grow system centered around proven industrial process control equipment. I love the arduino platform for hobby projects, and it certainly is a great fit for growers without a significant budget. I will explain in detail why i have made each of the equipment choices I've made, in the hopes that you the reader will understand why even though the price seems significant, the benefits counteract the initial investment.
The goal of the system is complete and total automation. What does that mean? Watering, feeding, lighting control, temperature control, humidity control, co2 control, ph control, and security. If marijuana was grown by multi billion dollar corporation, inside giant facilities, their systems would look and operate strikingly similar to what I intend to build, just on a much larger scale than my project. My grow system will be industrial hardened, capable of withstanding harsh environments and demanding situations. This entire thread will encompass the automation, instead of the growing. A grow journal will follow the completion of the project.
Lets start with a system summary. Including a budget. The budget for this project is 5 thousand dollars. Don't cringe, we have a lot to accomplish!
Equipment summary
PLC - The brain of the operation.
HMI - Human machine interface, a touch screen which allows user manipulation, for changing timers, PID loops settings, schedules, etc etc. The HMI talks directly to the PLC.
EC/ PH transmitter - This device sends information to the plc regarding current ph, and current conductivity.
co2 transmitter - this device sends information the the plc regarding the co2 levels at the sensor
temp/humidity transmitter - this device sends information regarding the temperature and humidity of the environment back to the PLC controller
Relays - to control the flow of power to devices
Liquid level sensors - to monitor reservoir heights
solenoid valves - to control water flow to the reservoir/hydroponic system.
Miscellaneous control wiring to the various remote devices
peristaltic pumps - to dose nutrients into the reservoir
I will go into more specifics of the project in a short while. But until those post start happening. I should probably leave you with a teaser to prove this project is happening, even as we speak...
Pictures are worth how many thousands of words? I'll try to do a little explaining with each picture....
This is an HMI. Its a 6 in Automation Direct touch screen interface. It retails for 699.00$ USD. Its ethernet capable, which means a user can connect the system to their home network and monitor the operator screens from anywhere in the world. It will display all current environmental levels, and allow for the input of schedules and desired levels. It has a built in html server which means you can custom design an accompanying website which loads much the same way a user logs in to control settings. It can send email alerts on any system variable. For instance if the ph drifts out of a range you will get an email letting you know, if the temperature exceeds a safety limit and the controller shuts the system down to prevent damage, it will send you an email to let you know. All screens, and the system itself can be password protected to multiple user levels.
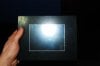
This is belden signal cable. When it comes to transmitters, and sending analog data, belden is the way to go. This is a 100' reel of 22 gauge 3 twisted, and shielded pair. I will be using it to transmit the analog signals from the ph/ec transmitter back to the plc. The foil shield and twisting of this signal pairs is what makes this cable so unique, and capable in an industrial setting, together these two features help to eliminate, RF, EMI, and other common mode disturbances, which can cause anomalies in any electrical system. All signals will be 4-20 mA signals. There are several industry standard control signals, the primary two being +-0-10v, and +-0-20 mA. I exclusively use 4-20 mA because of its resilience to electrical noise. My main concern with electronics in a grow room is electrical noise from digital ballasts. Proper grounding, and bonding, along with an aggressive noise control plan is key to preventing stray signals from negatively impacting your process. This is one of the reasons I cringe when I review arduino projects. Most arduino applications utilize voltage signals, including 0-1, 0-5vdc. These systems are incredibly susceptible to electrical noise. Because a 4-20mA loop relies on current, instead of voltage, there is a certain degree of inherent noise immunity. Retail 107$
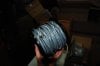
This is belden 2 pair twisted shielded cable, 100 ft. Retail 54$
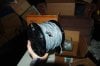
This is two nema 12 enclosures, one will house the PLC and HMI, the other will contain the ph/ec transmitter. A nema 12 enclosure is rated for dust, debris, and splash environments. Going to a nema 4x enclosure would also make them wash down rated, meaning you could literally take a garden hose to your grow controller. I don't plan on watering my controller, just the plants, but in a worst case scenario all of this equipment is splash rated, including the touch screen hmi. A third enclosure as large as the first will contain the outlets, and relays for controlling external devices, such as air conditioners, pumps, ballasts, etc. the 16x12x8 enclosures were bought for 79$ each, the 8x6x4 enclosure was purchased for 54$
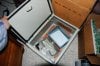
Simple enough: PH/EC calibration, cleaning, storage solutions. If you have a digital meter you've used these before. Made by Hanna Instruments.
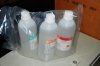
This is the ph/ec transmitter. It sends back 2 analog signals to the PLC controller. Both signals are 4-20 mA. Example: If the ph of the solution is 14, the ph signal is at 20mA, if the ph is at 2, the signal is 0 mA. This controller has galvanically isolated outputs to mitigate possible sources of noise back to the controller. The ph and ec probe are separate units. This transmitter retails for 400$ Made by Hanna Instruments.
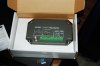
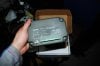
This is the EC probe, it sends an un amplified signal back to the ph/ec transmitter, which then processes that signal, and scales it to the output range. This probe retails for 130$. It should never need replacement. Made by Hanna Instruments.
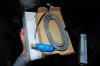
This is the PH sensor. It also send an unamplified signal back to the transmitter, which does all of the scaling before sending back a processed signal to the PLC. This probe retails for 125$. It should be replaced, like almost all probes, once a year. Especially since it will be submersed and measuring the ph 24 hours a day. Also made by Hanna Instruments.
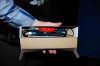
Relays, and Relay bases. For controlling the flow of electricity to the external devices. 100$ in miscellaneous wiring supplies. Automation direct.
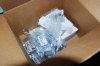
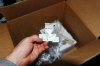
Terminal blocks, to make wiring less cluttered and more organized. Automation Direct.
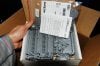
Relative humidity and temperature transmitter. It will send back 2 separate analog signals to the plc in the form of 4-20mA loops. Its measuring range is from 0-100 percent relative humidity, and -32 - 140 degrees Celsius. This transmitter is made by OMEGA engineering, it retails for 175$
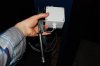
The BRAINS of the beast. This is a koyo/direct automation, DL06 PLC. It is capable in executing over a thousand boolean arguments in under a millisecond. It can control up to 8 P.I.D. Loops. It has expansion for up to 4 expansion cards. Slot one is occupied by an analog input module, this module can accept up to 8 different analog inputs, all 4-20 milliamp range. We have 1. Temp 2. Humidity 3. Ph 4. EC. 5. C02.. A total of 5 analog inputs. This controller is programmed with Directsoft programming software. The software bundle which includes all features retails for 495$. It can program any of the direct automation line of PLC's, including the DL05, DL06, DL205 series, DL305 Series, and DL405 hardware series. The Analog input card retails for 130$, and the DL06 PLC retails for only 239$... Even though the PLC is in charge of everything, it actually carries a very small part of the project budget. These controllers are VERY reasonably priced. So a total for the PLC including software and cards comes to 864$, add an analog output card for control of the dosing pumps and we round it to 1000$
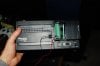
Questions and comments are welcome. In fact, they will drive the direction, and detail of this thread. I will continue to update the thread with the status of the overall project as I move through all of the developmental stages, up until the point its controlling a grow room. I will answer as many questions as I can. Thanks for checking it out, and I hope that someone can take something away from my experiences to improve their own. Cheers!
Lately I've been very intrigued with the D.I.Y. automation here on Rollitup. It is clear that RIU is a community of intelligent, driven individuals who are more than willing to share their knowledge and expertise. I applaud all of you who are continually striving to add integrity, knowledge, and ingenuity to the world of marijuana.
This thread is to be my opportunity to share my knowledge on growing, in the manner I am most capable of: Automation.
While many of you have undertaken Arduino projects, with great success, I will be developing a grow system centered around proven industrial process control equipment. I love the arduino platform for hobby projects, and it certainly is a great fit for growers without a significant budget. I will explain in detail why i have made each of the equipment choices I've made, in the hopes that you the reader will understand why even though the price seems significant, the benefits counteract the initial investment.
The goal of the system is complete and total automation. What does that mean? Watering, feeding, lighting control, temperature control, humidity control, co2 control, ph control, and security. If marijuana was grown by multi billion dollar corporation, inside giant facilities, their systems would look and operate strikingly similar to what I intend to build, just on a much larger scale than my project. My grow system will be industrial hardened, capable of withstanding harsh environments and demanding situations. This entire thread will encompass the automation, instead of the growing. A grow journal will follow the completion of the project.
Lets start with a system summary. Including a budget. The budget for this project is 5 thousand dollars. Don't cringe, we have a lot to accomplish!
Equipment summary
PLC - The brain of the operation.
HMI - Human machine interface, a touch screen which allows user manipulation, for changing timers, PID loops settings, schedules, etc etc. The HMI talks directly to the PLC.
EC/ PH transmitter - This device sends information to the plc regarding current ph, and current conductivity.
co2 transmitter - this device sends information the the plc regarding the co2 levels at the sensor
temp/humidity transmitter - this device sends information regarding the temperature and humidity of the environment back to the PLC controller
Relays - to control the flow of power to devices
Liquid level sensors - to monitor reservoir heights
solenoid valves - to control water flow to the reservoir/hydroponic system.
Miscellaneous control wiring to the various remote devices
peristaltic pumps - to dose nutrients into the reservoir
I will go into more specifics of the project in a short while. But until those post start happening. I should probably leave you with a teaser to prove this project is happening, even as we speak...
Pictures are worth how many thousands of words? I'll try to do a little explaining with each picture....
This is an HMI. Its a 6 in Automation Direct touch screen interface. It retails for 699.00$ USD. Its ethernet capable, which means a user can connect the system to their home network and monitor the operator screens from anywhere in the world. It will display all current environmental levels, and allow for the input of schedules and desired levels. It has a built in html server which means you can custom design an accompanying website which loads much the same way a user logs in to control settings. It can send email alerts on any system variable. For instance if the ph drifts out of a range you will get an email letting you know, if the temperature exceeds a safety limit and the controller shuts the system down to prevent damage, it will send you an email to let you know. All screens, and the system itself can be password protected to multiple user levels.
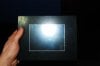
This is belden signal cable. When it comes to transmitters, and sending analog data, belden is the way to go. This is a 100' reel of 22 gauge 3 twisted, and shielded pair. I will be using it to transmit the analog signals from the ph/ec transmitter back to the plc. The foil shield and twisting of this signal pairs is what makes this cable so unique, and capable in an industrial setting, together these two features help to eliminate, RF, EMI, and other common mode disturbances, which can cause anomalies in any electrical system. All signals will be 4-20 mA signals. There are several industry standard control signals, the primary two being +-0-10v, and +-0-20 mA. I exclusively use 4-20 mA because of its resilience to electrical noise. My main concern with electronics in a grow room is electrical noise from digital ballasts. Proper grounding, and bonding, along with an aggressive noise control plan is key to preventing stray signals from negatively impacting your process. This is one of the reasons I cringe when I review arduino projects. Most arduino applications utilize voltage signals, including 0-1, 0-5vdc. These systems are incredibly susceptible to electrical noise. Because a 4-20mA loop relies on current, instead of voltage, there is a certain degree of inherent noise immunity. Retail 107$
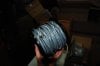
This is belden 2 pair twisted shielded cable, 100 ft. Retail 54$
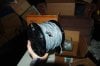
This is two nema 12 enclosures, one will house the PLC and HMI, the other will contain the ph/ec transmitter. A nema 12 enclosure is rated for dust, debris, and splash environments. Going to a nema 4x enclosure would also make them wash down rated, meaning you could literally take a garden hose to your grow controller. I don't plan on watering my controller, just the plants, but in a worst case scenario all of this equipment is splash rated, including the touch screen hmi. A third enclosure as large as the first will contain the outlets, and relays for controlling external devices, such as air conditioners, pumps, ballasts, etc. the 16x12x8 enclosures were bought for 79$ each, the 8x6x4 enclosure was purchased for 54$
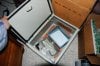
Simple enough: PH/EC calibration, cleaning, storage solutions. If you have a digital meter you've used these before. Made by Hanna Instruments.
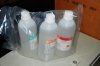
This is the ph/ec transmitter. It sends back 2 analog signals to the PLC controller. Both signals are 4-20 mA. Example: If the ph of the solution is 14, the ph signal is at 20mA, if the ph is at 2, the signal is 0 mA. This controller has galvanically isolated outputs to mitigate possible sources of noise back to the controller. The ph and ec probe are separate units. This transmitter retails for 400$ Made by Hanna Instruments.
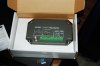
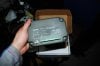
This is the EC probe, it sends an un amplified signal back to the ph/ec transmitter, which then processes that signal, and scales it to the output range. This probe retails for 130$. It should never need replacement. Made by Hanna Instruments.
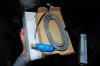
This is the PH sensor. It also send an unamplified signal back to the transmitter, which does all of the scaling before sending back a processed signal to the PLC. This probe retails for 125$. It should be replaced, like almost all probes, once a year. Especially since it will be submersed and measuring the ph 24 hours a day. Also made by Hanna Instruments.
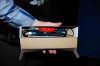
Relays, and Relay bases. For controlling the flow of electricity to the external devices. 100$ in miscellaneous wiring supplies. Automation direct.
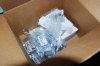
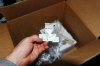
Terminal blocks, to make wiring less cluttered and more organized. Automation Direct.
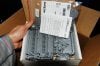
Relative humidity and temperature transmitter. It will send back 2 separate analog signals to the plc in the form of 4-20mA loops. Its measuring range is from 0-100 percent relative humidity, and -32 - 140 degrees Celsius. This transmitter is made by OMEGA engineering, it retails for 175$
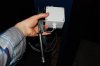
The BRAINS of the beast. This is a koyo/direct automation, DL06 PLC. It is capable in executing over a thousand boolean arguments in under a millisecond. It can control up to 8 P.I.D. Loops. It has expansion for up to 4 expansion cards. Slot one is occupied by an analog input module, this module can accept up to 8 different analog inputs, all 4-20 milliamp range. We have 1. Temp 2. Humidity 3. Ph 4. EC. 5. C02.. A total of 5 analog inputs. This controller is programmed with Directsoft programming software. The software bundle which includes all features retails for 495$. It can program any of the direct automation line of PLC's, including the DL05, DL06, DL205 series, DL305 Series, and DL405 hardware series. The Analog input card retails for 130$, and the DL06 PLC retails for only 239$... Even though the PLC is in charge of everything, it actually carries a very small part of the project budget. These controllers are VERY reasonably priced. So a total for the PLC including software and cards comes to 864$, add an analog output card for control of the dosing pumps and we round it to 1000$
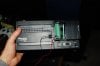
Questions and comments are welcome. In fact, they will drive the direction, and detail of this thread. I will continue to update the thread with the status of the overall project as I move through all of the developmental stages, up until the point its controlling a grow room. I will answer as many questions as I can. Thanks for checking it out, and I hope that someone can take something away from my experiences to improve their own. Cheers!