Hell yea! I'm just in veg right now so I can't comment on yield or nothin', but my plants seem to actually prefer the supplementals to my Warm White or Neutral White spotlights. They wanna grow towards the supp when both lights are same height and the plant is placed directly between the two.
I actually mounted my heatsink cores onto some of these:
http://www.ebay.com/itm/Winco-ALXP-1013-Sheet-pan-/350580879276#vi-content
Shipping is what kills you so finding a place that can combine shipping and won't rake you over the coals on postage fees is the trick. I also put some cheap heat sinks from eBay onto the back of those, but really, the 1W'ers don't throw much heat, ime, I don't even think they're needed (although you could add heat sinks if you find that they're necessary). The pans are very easy to drill so that you can feed the wires through to the face, but if you choose these pans make sure when you drill the hole you've got a block of wood or something underneath for support that you don't mind drilling into otherwise you'll get some tear out and warping. Definitely find a scrap of wood you don't care about. Now is also the time to drill holes on the sides so that you can hang the panel.
Now the driver, that throws all the heat. Definitely keep the drivers in a remote location unless you think the tent temps can stand to be raised a bit from ambient. I'm
adding light to my tent and I'm just about maxed out right now as far as temps are concerned. And that's with only two of the 30W supp's fired up and the 50W spotlight on. With the 20W/50W/100W spotlights all running, and all three 30W supp's I'm going to be
hurrrting... and it's winter (small closet). I'm going to have to work on this
for sure, but I just want to make a point that it's not a fun place to be. Be careful.
Merry shipped my units with these slabs of styrofoam that she cut a bunch of squares into so that the LED's can sit
within the styrofoam slab and not actually touch anything. I lathered premixed JB Weld (NOT the Quik Weld, the standard "steel" stuff, better thermal properties) onto the back of the heatsink core, placed it onto the frying pan, lined up the holes so I'd be able to feed the driver output wires to the front for soldering, and made sure everything was square. Then I placed one of the styrofoam slabs over the heatsink core and placed a 20lb weight over the styrofoam. This protects the LED's during this process and ensures good, quality contact between the two mating faces. Then I took a hairdryer and heated up the frying pan to the point where it was unconfortable to the touch. In my mind this was making sure the JB Weld layer was as thin as possible and there weren't any bubbles. It seems to have worked because my panel (both the heatsink core and baking pan) stay very cool
despite the fact that I mounted my drivers on the back. Make sure nothing slides around during this step.
Here's the back of my panel once finished:
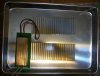
That was the first one I made. See the tear out where the wires are going through? My second and third panel are much cleaner. The heat sinks look laughably small, but they actually cover most of the heatsink core and were placed in such a way that they're as close to the highest number of LED's as possible. And, again, I highly doubt that I even need them.
Feel free to ask any questions.