stardustsailor
Well-Known Member
And some info about suggested Clamping Loads For the Vero series :
(Flat head screw ,w/o washer )
Vero 10 : 2 x M2.5 x 23 N*cm torque = 92 Kg total ( = 202.8 lbs )
Vero 13: 2 x M2.5 x 34 N*cm torque = 136 Kg total ( = 299.8 lbs )
Vero 18 : 2 x M2.5 x 34 N*cm torque = 136 Kg total ( = 299.8 lbs )
Vero 29 : 4 x M3 x 45 N*cm torque = ~300 Kg total ( = 661.4 lbs )
http://www.engineersedge.com/calculators/torque_calc.htm
*****With the use of flat washers , total clamping loads,
could be increased up to 5x,depending on the washers used.
(Wider washer = higher torque= higher clamping load. )
Of course ,this is allowed only for the Vero series ,of which the substrate is made from aluminium.
Regarding other types of COB arrays
with ceramic substrates -i.e. Cree CXA-CXB -there's no way ,
that such high clamping loads could be achieved / reached .
( My DIY V series : 1330+ kg !!! ( 2930+ lbs ) of total clamping load ,per Vero 29 )
The array will break in pieces ,as it is made of fragile ceramic material.
It gets clear ,that for high thermal performance of a high power COB ,the chosen substrate should be made from Aluminium or Copper ,as they offer high thermal conductivities-thus lower thermal resistance between junction & case- ,
while they are able to withstand excessive "clamping loads " from Array holders /screws ,
thus insuring better surface contact ,which results in higher heat conduction .
Ceramic substrate used for COB LED arrays , AlO =Aluminium oxide=Alumina ,is a bad choice for high power LED COBS.It is very fragile,not able to withstand high clamping loads ,as also it has poor thermal conductivity ,vs Aluminium or worse vs Copper.
- For comparison : Ideal CHIP-LOK 50-2234C array holder for CXA/B 3070 =
2x M3 x 0.5 N*m torque =166.66 kg total clamping load ( ~367.4 lbs ) . MAXIMUM -
But alumina has low heat expansion coefficient ,and thus a material with / of low mechanical stress ,due to heat cycling .
Still...
Higher thermal conductivity ,means better cooling .
Better colling means ,more efficient real-time operation( lower Vf droop ) .
Better cooling means higher light output maintenance,thus longer service life ( lower Tj ).
Better colling means higher efficiency at higher driving currents.
You'll be suprised ,when in real life surfaces contacting ,can be as low as 20% or even lower , of the "theoritical"surface area ,especially with low ( or w/o ) clamping load applied .
Like :
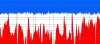
In blue color is the bottom ceramic super smooth surface of a Cree CXA3070 array .In red is the untreated
(only degreased ) aluminium surface,magnified many-many times ...
The white gap in between is supposed to be decreased by sanding the heat sink surface and/or apply lots of clamping force/load and of course what's left then ,to be filled with TIM .
Cheers.

(Flat head screw ,w/o washer )
Vero 10 : 2 x M2.5 x 23 N*cm torque = 92 Kg total ( = 202.8 lbs )
Vero 13: 2 x M2.5 x 34 N*cm torque = 136 Kg total ( = 299.8 lbs )
Vero 18 : 2 x M2.5 x 34 N*cm torque = 136 Kg total ( = 299.8 lbs )
Vero 29 : 4 x M3 x 45 N*cm torque = ~300 Kg total ( = 661.4 lbs )
http://www.engineersedge.com/calculators/torque_calc.htm
*****With the use of flat washers , total clamping loads,
could be increased up to 5x,depending on the washers used.
(Wider washer = higher torque= higher clamping load. )
Of course ,this is allowed only for the Vero series ,of which the substrate is made from aluminium.
Regarding other types of COB arrays
with ceramic substrates -i.e. Cree CXA-CXB -there's no way ,
that such high clamping loads could be achieved / reached .
( My DIY V series : 1330+ kg !!! ( 2930+ lbs ) of total clamping load ,per Vero 29 )
The array will break in pieces ,as it is made of fragile ceramic material.
It gets clear ,that for high thermal performance of a high power COB ,the chosen substrate should be made from Aluminium or Copper ,as they offer high thermal conductivities-thus lower thermal resistance between junction & case- ,
while they are able to withstand excessive "clamping loads " from Array holders /screws ,
thus insuring better surface contact ,which results in higher heat conduction .
Ceramic substrate used for COB LED arrays , AlO =Aluminium oxide=Alumina ,is a bad choice for high power LED COBS.It is very fragile,not able to withstand high clamping loads ,as also it has poor thermal conductivity ,vs Aluminium or worse vs Copper.
- For comparison : Ideal CHIP-LOK 50-2234C array holder for CXA/B 3070 =
2x M3 x 0.5 N*m torque =166.66 kg total clamping load ( ~367.4 lbs ) . MAXIMUM -
But alumina has low heat expansion coefficient ,and thus a material with / of low mechanical stress ,due to heat cycling .
Still...
Higher thermal conductivity ,means better cooling .
Better colling means ,more efficient real-time operation( lower Vf droop ) .
Better cooling means higher light output maintenance,thus longer service life ( lower Tj ).
Better colling means higher efficiency at higher driving currents.
You'll be suprised ,when in real life surfaces contacting ,can be as low as 20% or even lower , of the "theoritical"surface area ,especially with low ( or w/o ) clamping load applied .
Like :
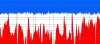
In blue color is the bottom ceramic super smooth surface of a Cree CXA3070 array .In red is the untreated
(only degreased ) aluminium surface,magnified many-many times ...
The white gap in between is supposed to be decreased by sanding the heat sink surface and/or apply lots of clamping force/load and of course what's left then ,to be filled with TIM .
Cheers.

Last edited: