In order to proper reflow tiny ceramic leds (Cree-Osram-Philips-etc ) and have a good result ,
solder paste has to be applied with the use of a stencil .....
Here's some tips / ideas ....
Proper -professional grade solder paste stencils are :
-laser cut ,
-at a trapezoid profile of ~5° ........ ( / _____ \ ) ......
-and with circular corners in pad design / cut ...
-Made of stainless stell sheet
( thickness varies depending led : from ~100 um to 150 um .
120um suggested for most leds ) ...
....
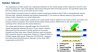
.....
If there's a company around ,that uses laser to make signs, metal decoration parts ,etc,
Make in Photoshop a led solder pad ,according to manufacturer's recommendations (found on leds spec pdfs ) ,at real size ,
and have your stencil professional grade made,for small amount of $ ....
Another way is to go and purchase from an Art's shop ,some copper foils/sheets ... (cheap ) ...
Used for artistic copper etchings ....
(Can you imagine ? " M.C. Escher Printed Circuit Boards Company LTD " ....

..... )
You can find them in plenty of available thicknesses ..( ~50 um to ~ 250 um or more .... ) .....
Make a leds's pad design with Photoshop ..
( Tools like -Rectangular shape -Smooth/Sharpen edges -fill -Invert ,might come handy ...)
In it's real dimensions at designing & printing sizing .....
Print it with laser printer ..And thermally transfer it onto copper foil/sheet ..
(background : toner full -pads : plain paper /empty )
Use packing tape to cover the rest of copper foil ...
Back ,sides,everywhere except on the print .
Make 100% sure that you've made a water-proof job !
Tape has to be firmly stuck with copper foil ...
Etch the thing ....
Now ,you have your own stencil ...
Thing is that it can not be used many times ..
It is made out of soft copper and will deform by time ,as several stencils will be made ...
Then you just have to make another ,new one ,same way ....
-Apply solder paste immediatly when taken out from fridge ..
(Solder paste is stored for up to 6 months in fridge .)
The colder (thick -hard-solid) the paste ,the more clean and accurate it will sit / stay,
after applied and stencil is removed ..
Working with such tiny apertures and warm solder paste ,can drive you crazy !
Trust me on that ....
-Cut a strip from an old cash / phone / credit card to use as a solder paste spreader ,over the stencil .
...0.5- 1 cm wide is nice ....
With some fine sandpaper ,work-softly/gentle- the edge ,to make it smooth ,without abnormalities and totally straight ..
-place/glue fine grain ( > #1000 ) sandpaper on a flat board and move/work the strip on the sandpaper .
Not the sandpaper over a still hand held or viced ,credit card strip -
A good,stiff ,flat ,smooth " spade " / " spreader " is crucial ....
-Get some fine tattoo needles ...!!!
Perfect for hand re-working/ trimming applied solder paste..
Clean the "gaps" between connections ,remove excess paste ,etc ..
-Use _grounded preferably _ a pair of tweezers to place the leds over the solder paste "pads " ....
Light handed ....Reallllyyyy gently ....
Just drop them ...
Do not "plant" them ,with force ....
Drop them over solder ,as close to their right position as possible .
Lightly push the leds at side of case ,with tweezer tip,to "trim" them in place ....
While reflowing ,solder will self-align the leds ....
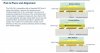
...
-Using a hot plate / stove plate to reflow leds ,once done couple of times starts to be fun and a piece of cake ....
In fact it is way easier than manually done ,hand soldering with a solder gun ....
You will start to reflow everything ,afterwards ....Solder gun will collect dust !
All the secret lies on solder paste stencil ....
Applied Solder paste,at pcb pad , has to be at right thickness ,even ,flat ,with no gaps / voids and precise .
If done correctly (delicate job,not difficult ! ) ,a close to perfect home-made reflowing is almost 100% guaranteed ....
-My personal approach in stencil applying is this :
a ) I work / " pass over " several times with the spreader per led .
Not just once .
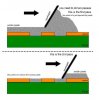
...=>
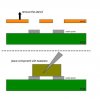
I use a small amount of cold solder paste ,placed in a small blob ,directly on the copper
stencil foil ,near the led pad "voids" of stencil ...
Then with the plastic card spreader,I work it from several directions ,until i get a good
filled ,flat and smooth solder stencil ....Then I remove the copper stencil /mask and move to the next led's pads ..
b ) I tend to use a "solo " led stencil strip ....
Not the whole array of leds printed on one single stencil sheet...
Difficult to place ,align and hold still ,while placing solder paste in many leds .....
So I use a thin strip ,with a single led pad stencil close on it's one tip end ....
It can be used for replacing single (fried) leds from a led array ....
Yes ,kinda slow work ,working each led stencil one by one ,
but it bewcomes rewarding ,while reflowing ....