noodle-led
Well-Known Member
As a followup. I am building my fixture and have 9x 560mm strips running on a HLG-185H-C1050. It pulls 205W at the wall, which given the 94% efficiency at 100% load for the driver is 192.7W delivered to the strips. Vf for the 9x array was measured at 177.6VDC or 1085mA. I'm just going to assume that given all the measurement tolerances, that's the rated 1050mA output. Oddly enough, attached to a 24"x28" sheet of aluminum flashing, they reach 56C stabilized temperature in still air, 51C with room air circulating. The strips are attached with 20mm thermal tape but I am thinking I am going to at least put some M4 screws in the ends for piece of mind.
Somewhat off topic, but how do these poke-in connectors work? I can't get a wire to stick inside of them. Am I supposed to... just poke the bare wire in? I've got solid core 20AWG wire which measures 0.8mm with a digital caliper so that's inside the range they're supposed to work. There just isn't any sort of locking.
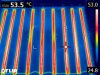
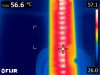
Somewhat off topic, but how do these poke-in connectors work? I can't get a wire to stick inside of them. Am I supposed to... just poke the bare wire in? I've got solid core 20AWG wire which measures 0.8mm with a digital caliper so that's inside the range they're supposed to work. There just isn't any sort of locking.