stardustsailor
Well-Known Member
Another Alternative for Epoxy :
Adtech ..
http://www.adtechplastics.com/pc-61...r-n-61-n-6-ceramic-filled-casting-system.aspx
http://www.adtechplastics.com/pc-54-38-el-336-high-temp-laminating-system.aspx
And it's ceramic fillers :
http://www.adtechplastics.com/pc-177-43-n-61-ceramic-powder-mix.aspx
http://www.adtechplastics.com/pc-176-43-n-60-ceramic-powder-mix.aspx
***The specific heat is the amount of heat per unit mass required to raise the temperature by one degree Celsius. The relationship between heat and temperature change is usually expressed in the form shown below where c is the specific heat. The relationship does not apply if a phase change is encountered, because the heat added or removed during a phase change does not change the temperature.
Adtech ..
http://www.adtechplastics.com/pc-61...r-n-61-n-6-ceramic-filled-casting-system.aspx
http://www.adtechplastics.com/pc-54-38-el-336-high-temp-laminating-system.aspx
And it's ceramic fillers :
http://www.adtechplastics.com/pc-177-43-n-61-ceramic-powder-mix.aspx
http://www.adtechplastics.com/pc-176-43-n-60-ceramic-powder-mix.aspx
...that improve filler compaction and 'specific heat'* properties of...
***The specific heat is the amount of heat per unit mass required to raise the temperature by one degree Celsius. The relationship between heat and temperature change is usually expressed in the form shown below where c is the specific heat. The relationship does not apply if a phase change is encountered, because the heat added or removed during a phase change does not change the temperature.
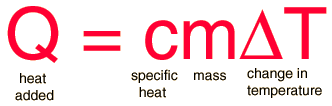