AquariusPanta
Well-Known Member
What's up fellow RIUians. I wanted to make a thread on thermal readings, as I haven't seen hardly anyone document thermal readings for their cob units, whether through commercial or DIY and I find it to be very important for us who want our lights operating at optimal temperatures. From what I can gather, it's uncharted territory for a bunch of us here and hardly anyone has yet attempted to fully enlighten others regarding this kind of procedure; I'm here to do just that with this video:
Here are some readings I recorded recently:
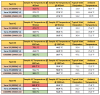
As you can probably tell, there's an obvious anomaly with the sample #1 for the Vero 29, as it gets progressively hotter throughout the testing period. While testing, I held up my Apogee PAR meter underneath both samples at equal distances and positions and read similar outputs, so I knew then and there that something had become loose and that the thermocouple had been absorbing blank-range heat from the LES.
Also important to point out is that the Vero 29 runs a little more aggressively than it's Cree counterpart, thus explaining a little on why the CXB3590 runs cooler. Throw in the math that it also has a higher efficiency range than the Vero 29, there's no question on why the CXB3590 runs as cool as it did in these testings. All samples were ran with 120mm fans at 5V.
Anyways, I'd like to see other's attempts at recording and sharing their own thermal data, so please feel free to share any data that you have and remember that the more variables listed, such as ambient temperature, the better the rest of us will make of that input.
Here's a link to the digital thermometer from the video:
http://www.ebay.com/itm/400542887700?_trksid=p2060353.m2749.l2649&ssPageName=STRK%3AMEBIDX%3AIT
Here are some readings I recorded recently:
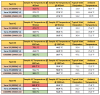
As you can probably tell, there's an obvious anomaly with the sample #1 for the Vero 29, as it gets progressively hotter throughout the testing period. While testing, I held up my Apogee PAR meter underneath both samples at equal distances and positions and read similar outputs, so I knew then and there that something had become loose and that the thermocouple had been absorbing blank-range heat from the LES.
Also important to point out is that the Vero 29 runs a little more aggressively than it's Cree counterpart, thus explaining a little on why the CXB3590 runs cooler. Throw in the math that it also has a higher efficiency range than the Vero 29, there's no question on why the CXB3590 runs as cool as it did in these testings. All samples were ran with 120mm fans at 5V.
Anyways, I'd like to see other's attempts at recording and sharing their own thermal data, so please feel free to share any data that you have and remember that the more variables listed, such as ambient temperature, the better the rest of us will make of that input.
Here's a link to the digital thermometer from the video:
http://www.ebay.com/itm/400542887700?_trksid=p2060353.m2749.l2649&ssPageName=STRK%3AMEBIDX%3AIT